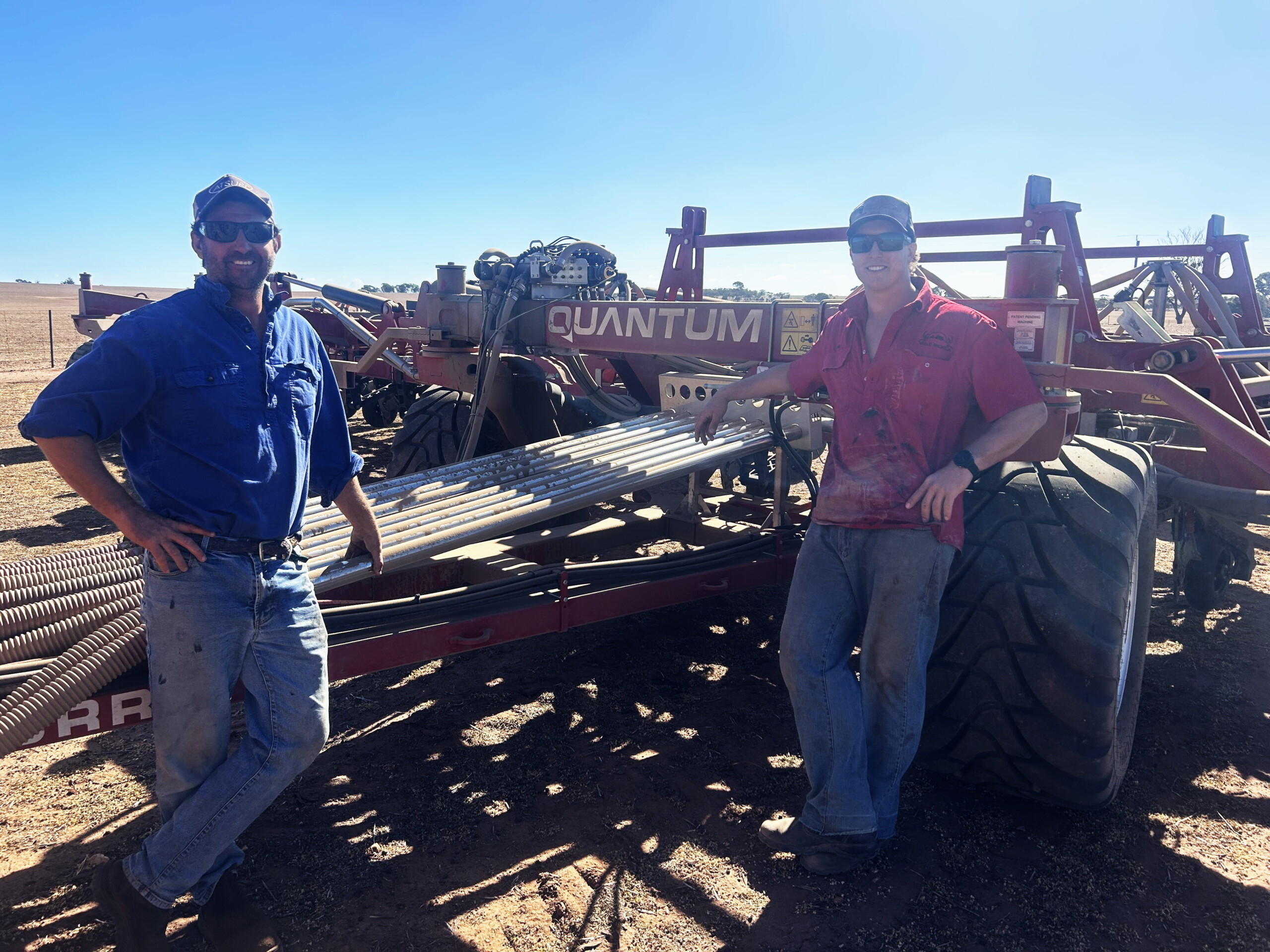
Photo caption: Kulin grower Jay Robertson and his nephew Seb Omodei with the family’s new 18-metre Morris Quantum air drill during the recent seeding season.
WITH a 21-metre seeding bar causing their tractor to groan a little in tough conditions and consequently impacting soil chemical throw, the Robertsons near Kulin were left with the choice of investing in a bigger tractor or a smaller bar.
They chose the latter, however they certainly didn’t want to change their bar brand and this resulted in delivery of a new 18m Morris Quantum air drill prior to seeding.
Jay Robertson, together with his wife, Alecia, and parents, Graeme and Tricia, crops 3800 hectares of their 5200ha ‘Jesmond Farm’ property plus leased land to wheat, barley, oats, lupins and canola. Jay and Alecia have four children, Tate (16), Fraser (14), Oliver (12) and Macey (10).
The family also runs a 7700-head sheep flock, including for crossbred lamb production, and, as a result, it plays a key role in their paddock rotations, particularly on the home property.
“We continuously crop good country, but we are gradually moving to more year-in-year-out with various paddocks on our home property,” Jay said.
Soils include mostly good loamy country, but also ranging from lighter sands through to grey clays and ironstone.
The Robertsons upgraded to their previous 21m Morris Quantum air drill, a demonstration model, from a 15m Flexi-Coil bar that had been extended to 16.8m, and they coupled their latest 18m Quantum bar to their existing Morris 9652LL air cart. The new air drill was pulled by their New Holland T9 tractor that was tuned to 615-horsepower.
Jay said despite switching to a slightly smaller bar, they were keen to achieve more consistent sowing speed and better soil throw with their seeing program.
The new Quantum air drill was configured similarly to the 21m model, with tines set at 30-centimetre spacings and the knife point and press wheel system delivering seed and granular fertiliser together and banding liquid fertiliser below the seed zone.
“Our demo model had done plenty of work when we got it in 2019 and it did some really heavy-lifting thereafter, but it certainly proved itself,” Jay said.
“We got all the early improvements done by McIntosh & Son to make it better on-the-go, which gave you confidence in the product they’re selling.
“The Flexi-Coil bar was spring-loaded, so with the hydraulic bar we were able to start seeding a little earlier, and the seed placement has been the big leap for us. It (the Quantum) knows where it should be, whereas with the spring tines, you can be just placing seed on top and feeding the birds on the ground.”
He said the Morris Auto-Pack technology, which automatically adjusts packing pressure according to soil conditions, also had played a key role in the improved seeding accuracy.
“We still use the hydraulic pressure quite a lot, but the pressing of the press wheel follows the ground and ensures you’re not burying seed in the softer soils or battling to get it into the harder country.”
“We’ve had a lot more even crop germination and establishment, and the paddocks are staying cleaner (with the better crop competition).
“We’ve certainly had some of our best yields the last few years. Last year, we had 60-millimetres (of rain) in March, so we had moisture down below, and then it dried-out a bit, but the placement was good and there was enough moisture. We only had 220mm for the year, and the leased land to the west got an extra 50mm, but our yield averages at home were not far off the leased farm.
“It’s about getting it in at the right time and in the right spot with that accuracy. You’ve got to be able to get that precision with seeding.”
Jay said the Morris Auto-Lift system for automatic lifting and lowering of tines, plus other technologies like end-of-row turning and blockage monitoring, now made the seeding job easier for operators.
“Last year we had an American backpacker and I only had to spend half a day with him and he did the rest.”
The Robertson’s tow-between Morris 9652LL air cart, comprising two 5000-litre liquid tanks and two granular tanks, was a step up from an older 8300L Morris air cart plus 12,000L liquid cart, which Jay confessed was a bit of a road train, not to mention he is now avoiding a tow-behind unit and the associated compaction.
They now complete about 110ha per fill, compared with 70-80ha previously.
Jay said the Morris carts were known for their simple calibration and metering accuracy, applying product rates as low as 2 kilograms/ha, plus their easy cleanouts.
He said the family was yet to move to full variable rate control and section control, however, they were preventing liquid application overlap via a liquid monitor mounted on their Quantum bar.
They also have switched from using flat fan heads to Raycol heads, as well as to the use of friction flow tube, which was avoiding the use of annoying joiners and limiting previous blockages.
Jay said the support for their Morris equipment from the McIntosh & Son team at Kulin had been excellent.
“What we have to look at with any machine is the service and attention. Since McIntosh & Son have come to the district, we can’t fault them,” he said.